Product Quality Inspection System and Control Procedure
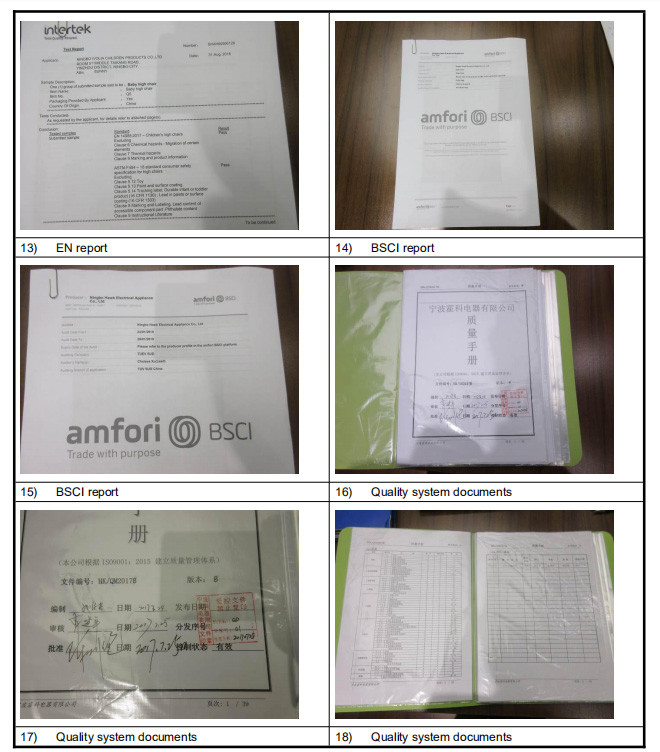
Product Quality Inspection System and Control Procedure
1. The basic responsibilities of quality management are as follows:
A/ Responsible for the quality inspection of raw materials, external parts (external processing parts, external rough parts), blanks, semi-finished products, finished products, until the finished products leave the factory. B/ Implement the principle of non-outflow of defective products to ensure that the products delivered meet the required standards and technical requirements. C/ Responsible for calibration and management of various quantities, measuring instruments and instruments. D/ Responsible for customer complaints, bad feedback and other analysis and processing. E/Responsible for the use of statistical techniques only and the collation of various inspection reports. F/ Responsible for staff's education planning and training on product quality. G/ Establish inspection standards for all kinds of products. H/ Records of quality assurance, inspection execution and physical and chemical analysis of various feeding processes.
2. Inspection work should strictly implement quality standards and inspection system. Inspectors should inspect products according to the requirements of product drawings and technical documents, make correct judgments and do a good job in the management of defective products.
3. Inspection work should focus on prevention, adhere to the first piece inspection, attach importance to process inspection, and strictly complete inspection. Machine plus operator must achieve "three words". (i.e. look, do and measure; A / check the defect of the next generation of processed parts before boarding machine; B / confirm before boarding machine; C / measure whether it meets the requirements after boarding machine. ) The quality inspection of key processes, key parts and key products should be strengthened, and quality records should be established and filed.
4. Inspectors should strive to do a good job of "three personnel" (quality inspectors, quality propagandists and quality analysts) in inspecting process operation rules, implementing the implementation, promptly dissuade violations of operation, and report to the head of the Department if necessary, and take prompt measures.
5. To organize random checks of stocks, qualified semi-finished products and finished products from time to time to assess the quality of inspection work.
6. Do a good job in measuring physics and chemical work, strict measuring instruments, periodic verification and maintenance.
7. Quality inspection of production process;
A/Inspectors in all links shall inspect the qualified products according to the requirements of product drawings, technical standards and process regulations. The qualified products shall be signed by the inspectors and then flow into the next process with the Product QC Engineering Form. The defective products shall be submitted to the Quality Control Department for formalities. Before inspection, inspectors should first understand the product, understand the process, determine the inspection quantity in the responsible area, and flexible inspection methods.
B/The inspection of all production links should emphasize "first inspection", strengthen "patrol inspection", strictly "final inspection" and "self-inspection" by operators.
(1) First Inspection: Every design change, mass production and trial production must be inspected. The first inspection shall be submitted to the first inspection after the operator has passed the self-inspection. After the first inspection is qualified, the inspector shall sign and affix the product exclusive stamp on the Product QC Engineering Form and the Daily Inspection Form so as to permit batch processing and production. The inspector shall be responsible for the products after the first inspection.
(2) Patrol inspection: Repeated in the production process, inspectors 2 hours/time, do a good job of patrol records, and be responsible for patrol products. In principle, sample inspection is carried out for batch products, with a rate of not less than 10%. If defective products are found during sample inspection, the reasons for the defective products should be judged timely and accurately and reflected to the head of the department. During inspection, the operator must also be checked whether he works according to the requirements of the process.
(3) Final Inspection: After the end of the process, the product is processed after deburring, iron scraps and oil pollution. If the product is found to be unclean, it has the right to return to the workshop for self-inspection and re-inspection. Inspection records should be made when inspecting, and key dimensions of main products should be carried out according to the requirements of inspection records.
(4) Self-inspection: The operator carries out self-inspection on the products processed by himself and plays the role of self-supervision. The bad products should be identified immediately and separately. Hand in the inspector for review and post-processing. C/All cross-sectoral processing processes (products) must be signed by the head of the processing Department on the "QC Project Form for Products", otherwise, the next process can be rejected.
8. If it is found that the production process violates the process regulations, the inspector shall promptly dissuade it. If the act seriously affects the quality of the product and the dissuasion is invalid, the inspector shall have the right to stop it and report it to the head of the Department and the head of the quality department immediately.
9. All production links within the division should insist that unqualified raw materials should not be used; unqualified products should not flow into the next process; unqualified products should not flow out of the company.
10. The finished products must be cleaned, rust-proof and oil seal as required before they are put into storage. The product inspector's signature on the Product QC Engineering Form is required for storage.
11. Bad products shall be handled in accordance with the relevant provisions:
A/Products that are judged to be defective by final inspection of finished products must be identified and classified and placed in warehouses for unified treatment by warehouses.
B/Whoever conceals or disposes of waste products privately and intentionally evades responsibility shall be dealt with seriously and given disciplinary sanctions.